NPK Fertilizer Production Technology
NPK fertilizer production technology we apply in our powder or granular ferilizer production lines is for quality compound fertilizer production. For example, we have 3 main techniques respectively in NPK fertilizer blending line, wet granulation line and dry granulation line. Also, we have special technologies for each NPK fertilizer production stage from crushing, granulating to bagging. Additionally, if you want to effectively make compound NPKs with more nutrients and market competitiveness, you can consider our fertilizer manufacturing equipment. Because of superior workmanship and extensive expertise our industrial technologies, our npk fertilizer equipment is the leading in the fertilizer industry.
Some fertilizer businesses and investors planning to set up a organic fertilizer plant should pay particular attention to understanding the fertilizer production plant cost. Moreover, the expenses involved in establishing such a organic fertilizer factory include land rent, plant construction, fertilizer production equipment, costs of raw and auxiliary materials, labor, energy consumption, return on investment, and more. Depending on the type of raw materials and the desired output, we can provide customized solutions for the production of organic fertilizer powder or granules or liquid fertilizer. All in all, these fertilzizer manufacturing plans cater to clients with equipment budgets ranging from $30,000 to $550,000.
Wet NPK Fertilizer Production Technology
As a matter of fact, wet granulation for NPK fertilizer manufacturing plant utilize the agglomeration method to make powdered materials sueezed into balls. Furthermore, this process needs by means of water or liquid binders. This wet NPK fertilizer granulation technology is suitable for large-scale compound fertilizer producers who seeking efficient and high-capacity NPK fertilizer production methods.
Hence, our plant develops two NPK wet granulation techniques: rotary drum granulation and disc granulation. What’s more, they are ideal for producing high, medium, and low concentration compound fertilizer pellets with the huge capacity of even more 20-40 t/h.
Top 2 Wet Granulators in NPK Fertilizer Production Process
Our company offer two types of wet granulators for NPK fertilizer manufacturing. Additionally, you can decide whether to install a water-spraying device. You can select two pelletizers based on compound fertilizer production output, land area, and budget. So we can also customize them according to individual needs.
In most cases, when producing large scale NPK fertilizer granules (over 10 t/h), we recommend combining one drum granulator with several disc granulators. This setup optimizes production efficiency and ensures the roundness of the finished granules.
How to Produce High-quality NPK Pellets by Wet Granulation Technique?
Wet granulation plays a critical role in NPK fertilizer production technology by transforming many raw materials into quality pellets. By reasonable planning, you can continuously feed main NPK raw materials into a rotating disc or drum during the wet granulation process. And we have device to spray water solutions and adhesives to help form fine powder into NPK fertilizer pellets, which offers significant benefits in the NPK fertilizer granulation.
Dry NPK Fertilizer Granulation Technique
Typically, dry granulation technology for NPK fertilizer pellet manufacturing applies the extrusion method to make solid or powder materials agglomerate by external pressure. Specifically, double roller extrusion is the most common method of producing NPK compounds granules. In particular, this technique is advantageous for customers with tight budgets, as it eliminates the need for costly drying processes and reduces energy consumption. Additionally, it benefits NPK fertilizer production businesses who require uniform NPK particle size and want to produce popular granular shapes in the market.
Which Equipment Use Dry Granulation Technique to Make NPK Fertilizer Granules?
You can utilize the NPK fertilizer dry granulation technology to produce high-quality granules. The key equipment in this process is the double roller extrusion granulator. It has won the praise of the majority of users since its launch! We’re having a sale, and buy now to enjoy more!
In summary, the double roller extruder granulator is the ideal equipment for the NPK fertilizer dry granulation process. We offer high-quality machines that are cost-effective and customizable to your production needs. You can contact us to learn more about how our technology can enhance your fertilizer production.
What Are the Benefits of Dry Granulation in NPK Fertilizer Production?
Dry granulation is an important technique in granular NPK fertilizer production. So why we suggest small and medium NPK fertilizer plant to try dry granulation technology?
What Raw Materials You Can Use in NPK Dry Granulation Process?
We have identified some raw materials suitable for NPK fertilizer dry granulation technology. These materials can form compound fertilizer granules under physical pressure without or with little water. For example, superphosphate, potassium chloride, and potassium sulfate powders. Because these NPK powders have high granule hardness, low water solubility, and do not easily dissolve, making them ideal for direct dry granulation processes.
In summary, the physical and chemical properties of raw materials, such as hardness, particle size, moisture content, and adhesion, directly impact the performance of the double roller compact granulator in NPK dry granulation technique. By appropriate raw material pretreatment and process control, you can make high quality compound fertilizer pellets with great particle strength.
Type 1: NPK Blended Fertilizer Process for Compound Fertilizer Plant Design
Primarily, NPK blended fertilizer production line is a set of equipment and processes for BB fertilizer manufacturing. Besides, it usually includes crushing, batching, mixing and packaging steps.
If you are opening a new NPK fertilizer factory and have limited production experience, you can choose SX bulk blending fertilizer production line.
In fact, this technology is simple, and no drying or granulation processes. As a result, you needn’t purchase the relevant dryer or granulator. Accordingly, you can save a lot of money to prepare equipment. What’s more, in comparison to the other two techniques, its initial investment costs are relatively lowest.
For this, we offer several models for your actual production needs with the capacity of 5 t/h, 10-15 t/h, 20 t/h, 50-60 t/h, or 60-80 t/h. In addition, this NPK fertilizer production technology doesn’t take up too much workshop areas. Also, almost 500-3,000 ㎡ is enough.
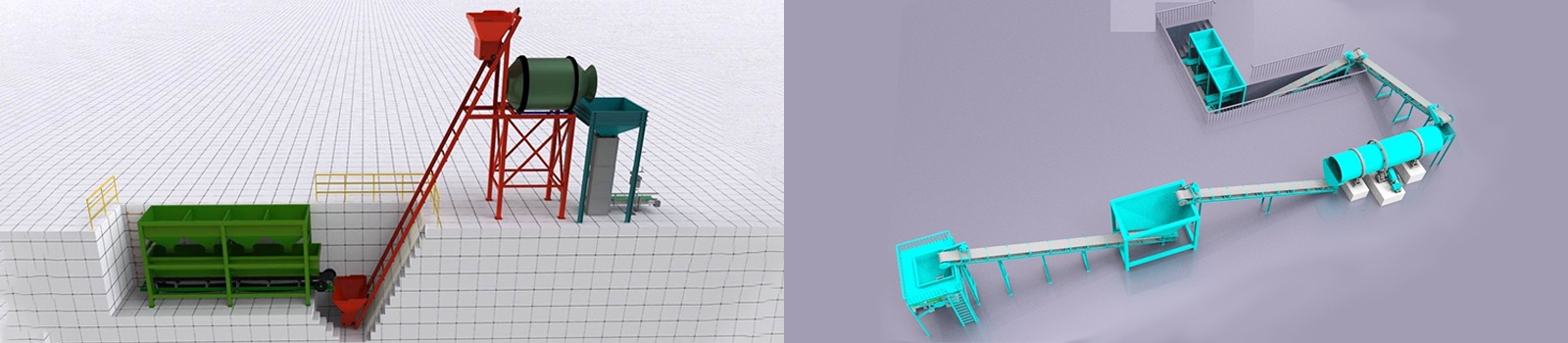
Bulk Blended Fertilizer Line For NPK Mixtures
The core machine in this blending technique is rotary drum mixer. To provide our customer better production effect, we have two types: BB fertilizer mixer & drum type BB fertilizer mixer.
BB fertilizer mixer designed by our engineers is controlled by switches and can automatically feed, mix, and discharge without the need for manual assistance. Additionally, single blender’s footprint is small, only 10 ㎡. Also, its production capacity is 5-10 t/h, and the price is affordable, which is suitable for small-scale NPK mixed fertilizer production. If you want the larger output, you can purchase multiple BB fertilizer mixers for working simultaneously, and we will give you a 10% discount.
And we have another drum type BB fertilizer mixer, which is available for achieving continuous production and large scale NPK fertilizer production with the rehular capacity reaching 30-40 t/h. More importantly, our equipment can mix up to 300 tons of NPK blending fertilizers per hour.
Then, by exact batching and blending several single element fertilizer or compound fertilizer in a certain proportion, you can get fertilizers with balanced nutrients.
Top 3 Crushing Techniques in NPK Fertilizer Production
In NPK fertilizer production, crushing is an important process to break compound NPKs into smaller particles for better mixing and granulation. Thus, there are three common crushing techniques, which are urea grinding, cage grinding and chain grinding technology.
This technology can break larger urea pellets and convert into fine powders to facilitate subsequent mixing and granulation processes. Typically, this method usually uses the gap between the roller and the concave plate to grind and cut urea particles into 0.3-0.5 mm. When it comes to capacity, SXNS-80 can dispose 5-8 tons of raw materials per hour, with the inlet moisture of less than 5%.
Cage crushing technology is suitable for grinding soft and brittle materials, such as industrial furnace slag, shale, medium hard coal, etc. Also, it can play a role in mixing and crushing multiple raw materials at the same time. In fact, the cage crusher has loose requirement for the raw materials’ water content, generally within 12%. When it comes to capacity, SXLSF-800 can process 6-10 t/h materials with 0.2 mm in size.
The last technique is suitable for crushing blocky and hard objects into less than 3 mm in compound fertilizer production like phosphate rock, coal, limestone, etc. For instance, our engineer develops two types of chain crusher. One is single shaft vertical crusher with the capacity of 2-3 t/h and the cheap price of $900. Besides, another equipment has two shafts with the largest capacity in NPK fertilizer crushing of 10-15 t/h.
These crushing techniques have a significant impact on breaking down raw materials into the desired particle sizes for further processing in NPK fertilizer production.
Top 2 Batching Techniques for NPK Compounds Processing
When it comes to the batching technology in NPK fertilizer production, our company has designed dynamic and static batching machines to ensure that the ingredient-mixing process has an error of less than 0.01. Besides, both of these machines have unique characteristics and applicability.
How to Fomulate 15-15-15 NPK Compound Fertilizer?
Taking a common NPK fertilizer formula as an example. Firstly, the proportion of NPK is 15-15-15, which means that the content of 15% N, 15% P2O5 and 15% K2O. Here are some details of this formula.
- Urea (nitrogen content 46%): Adding about 32.6%.
- MAP (phosphorus content 61%): Adding about 24.6%.
- Potassium sulfate (potassium content 52%): Adding about 28.8%.
- Other fillers and trace elements: Adding about 14%.
In the actual batching process, an operator will add various raw materials to dynamic or static batching machine according to the corresponding NPK ratio of the specific formulas. Then, you can add the necessary auxiliary materials to meet the requirements of the finished fertilizers. Additionally, the advanced control system automatically calculates the amount of each NPK component and strictly monitors the ratio during the batching process. Thus, this ensures the accuracy of the NPK ratio of 15-15-15.
Of course, we will ask the customer in advance if they are considering an automatic feeding system to reduce human intervention. As a result, this high-precision batching technology makes the NPK fertilizer production process more reliable and efficient, meeting the needs of different industries, including professional users in agriculture, horticulture, and soil improvement.
How to Make The Best Ratio in NPK Fertilizer Production Process?
In most cases, NPK ratio (N:P2O5:K2O) is 1-1-1 (e.g.15:15:15 or 20:20:20) will provide all of the nutrients that all plants require for optimal growth. Besides, here are some formulas for NPK fertilizer prodution are as follows/
Besides, you can make the NPK mixtures ratio of 4-2-3 or 4-3-2 for full growth period of crops.
Fertilizer factory can raise phosphorus content, like 1-2-1 NPK fertilizer ratios.
You can increase potassium ratios to 1-1-2, 1-2-2, or 2-1-2.
NPK fertilizer factory need to achieve 2-1-1 or 3-1-1 fertilizer ratios.
If you want to make accurate compound NPKs proportion, you need more than one high-quality batching machine. However, if raw materials contain large pieces that are difficult to handle, like DAP or other phosphorus sources, you should crush them firstly.
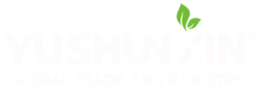
Get Free Quote Now!
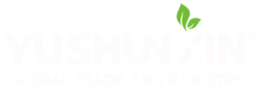