Granulator is one of the main equipment for processing finished fertilizer. And in the face of all kinds of granulating machines on the market nowadays, how to choose fertilizer granulator becomes a heated issue for the new investors who are involved in the fertilizer production business. This page will provide references for the initiates in the fertilizer industry.
What Factors Do You Need to Take Into Account in The Selection of A Pelletizer?
Ⅰ. Focus on Granulation Techniques— Dry Granulation vs Wet Granulation
1. Dry Granulation Machines
The moisture of the material is the primary control index for the pelletizing process. For one thing, dry granulation manufactures fertilizer pellets with relatively low material moisture. In general, the moisture content is less than 10% as a critical value, and there are very few materials can reach 16%.
For instance, extrusion granulators (flat die granulator and roller extrusion granulator) apply this method for the production of pellets in variable shapes. Compared with the wet granulation, it has lower energy consumption and equipment cost. Besides, it doesn’t require the dryers or binders to affect the nature of the materials.
2. Wet Granulation Machines
For another thing, wet granulators are equipped with sprinkle system. Moreover, we greatly recommend conditional fertilizer plants to utilize steam humidification for better granulation effect. Then, the following way is hot water granulation, which is superior than cold water granulation.
More importantly, wet granulation refers to the production of fertilizer particles containing 20-40% moisture, which are mostly in the form of balls. Furthermore, wet granulation has a variety of equipment: new type organic fertilizer granulator, rotary drum churning granulator, disc granulator and rotary drum granulator.
Note: High moisture of materials easily produce big spherical particles, while low moisture obviously cause fertilizer powder loose or sandy and lower granulation rate.
Ⅱ. Focus on Physical Properties of Raw Materials
Generally, before granulating, the size of feeding material should be less than 300 meshes which can be pelletized by rotary type granulators, such as churning granulator, drum granulator and disc granulator.
Flat die granulator or rotary roller extrusion granulator can make granules from materials with large size, forming difficulty and great hardness.
Light powder materials, such as livestock manure, coal dust, clay, and kaolin, require the addition of water or a binder to be formed granules. They can be granulated by a new type organic fertilizer granulator, disc granulator, or rotary drum granulator. All of these machines have liquid spraying device.
Furthermore, the extrusion granulator is suitable for granulation of non-viscous particles to avoid clinging to the roller sheet and affecting the working situation. For example, the equipment can use to dispose crude fiber materials, which are difficult to form with low adhesion, such as sawdust, rice husk, cotton stalks, cottonseed skins, weeds and other crops, straw and plant waste.
Ⅲ. Focus on Finished Products Requirements
1. Fertilizer Category
2. Fertilizer Granular Size
The particle size of the product obtained varies greatly depending on the granulation method. For example, rolling granulation commonly make pellets in the small and uneven size, usually 0.3-3mm, such as drum granulator and pan granulator. Nevertheless, the extrusion granulator make the size of the particles small and uniform through the mold, generally 2-10mm.
Moreover, other granulators can change the particle sizes by adjusting different parameters. Let’s take the disc granulator as an example!
How to Control The Particle Size of Disk Granulator?
3. Fertilizer Shape
Spherical pellets are processed by disc granulator, new type organic fertilizer granulator and churning granulator with high granulation rate, but drum granulator’s pelleting rate is low, only 70%. At present, large and medium scale fertilizer production factories mostly use rotary drum granulation machine. There are also some factories will connect disk granulator with drum granulator for secondary granulation, with better results.
Flat die granulator produces columnar granules.
Rotary roller extrusion granulator can make pillow shape, semicircle shape, stick shape, pill shape, walnut shape, flat ball shape and square bar shape. If you want spherical fertilizer granules, we recommend you to add organic fertilizer polishing machine.
Ⅳ. Focus on Capacity
If the output is 1-3 tons per hour, we suggest to choose flat die granulator or rotary roller extrusion granulator. If you require high effect of granules, you may choose the latter one.
For small production lines with an output of 4-8 tons per hour, we recommend choosing churning granulator or disc granulator. If you want better effect on the granules, you should choose the former. If you prefer high production efficiency, we advise you to install more than two disc pelletizers because of the low cost.
The drum pelletizer is generally ideal for professional medium and large organic fertilizer manufacturing plants with output requirements ranging from 9 to 30 tons per hour. If you require high capacity and good shape of the pellets, you can choose the rotary drum churning granulator.
In other words, if you own a small or medium scale fertilizer factory with an annual capacity of 5,000-20,000 tons, we propose a high-quality, low-cost flat die granulator and disc granulator. Furthermore, if you run a large fertilizer plant with an annual output of more than 50,000 tons, we recommend purchasing a rotary drum granulator directly. Because it is specifically designed to produce fertilizer granules on a greatly large scale and is more time-saving, efficient, and energy-efficient than several churning granulators working at the same time.
Ⅴ. Focus on Investment Costs
We strongly recommend you to choose flat die pelletizer and roller extrusion pelletizer because they are small in size, save civil construction cost and have good economic efficiency. They produce pellets in room temperature, without dryer and cooler, and have no environmental pollution. Meanwhile, they have high granulation density, high organic matter content and good fertilizer efficiency.
If you do not have a large budget and have severe environmental protection standards, we recommend that you choose a disc pelletizer, which has a low cost, low civil construction cost, a specific output, and can work more than one at the same time.
In conclusion, when choosing a right granulator, the fertilizer manufacturers need to consider their output and production cost. The granulation production process, in addition to the physical properties of the materials, is also closely related to the type and mechanical features of the granulation equipment.
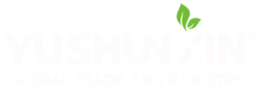
Get Free Quote Now!
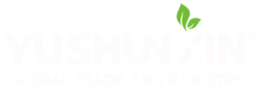