NPK Fertilizer Granulator
What Are The Raw Materials Suitable for NPK Fertilizer Granulator?
Generally speaking, NPK fertilizer contains at least two or three nutrients (nitrogen, phosphorus and potassium). It has the advantages of high nutrient content, small side effect and good physical properties.
Raw materials for NPK fertilizer production are mainly divided into three categories, including some fillers like clay.
- Nitrogen fertilizers: ammonium chloride, ammonium sulfate, urea, calcium nitrate, etc.
- Potassium fertilizers: potassium chloride, potassium sulfate, plant ash, etc.
- Potassium fertilizers: (heavy) calcium superphosphate, calcium-magnesium phosphate, phosphorite powder, etc.
Top 2 Granulation Techniques for NPK Fertilizer
NPK compound fertilizer granulation technology can be divided into wet and dry granulation. The distinction between them is whether or not the liquid solution is used. Dry granulation does not require the use of liquid solutions such as water or binders, whereas wet granulation must add liquid binders to the powder mixture.
Dry Granulation — Extrusion Granulation Technology
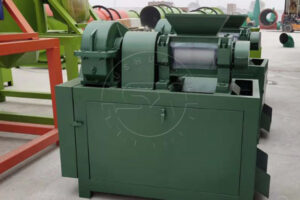
Double Roller Granulator
Due to the production of NPK fertilizer without water and binders, the traditional dry granulation technology is extrusion granulation. In the extrusion granulation process, high pressure makes solid materials polymerize into powder and squeeze between rollers to make fertilizer granules.
All finished fertilizer pellets do not require drying and cooling and can be packaged directly. As a result, the dry granulation method and associated equipment make up a small production line capable of forming a continuous, mechanized, and automated production with a certain capacity.
Our plant designs double roller extrusion granulator which suits for producing NPK Fertilizer granules.
The double roller extrusion granulator is the most common equipment in extrusion granulation technology.
- It is an equipment that crushes the material through a pair of relatively rotating extrusion rollers to form the required size of granules.
- The extrusion process converts the crushed materials into flakes. Then, this machine uses the crushing rollers to pulverize in the broken studio. Finally, after screening, you can obtain the finished products.
- Capacity: 1-2t/h.
- This series of granulators, you can select the shape and size of ball socket on the roller sheet according to the your needs. We can make pillow shape, semicircle shape, stick shape, pill shape, walnut shape, flat ball shape and square bar shape.The flat ball shape is generally well-sale.
- It widely occurs in dry powder granulation in fertilizer, feed and chemical industries, as well as rare earth, metallurgy, and coal.
- This extrusion granulation process is short and does not require drying and cooling, cutting input and operational expenses.
- High finished products rate and granulation ratio up to 95%. Despite their coarse surface, fertilizer granules have good curing property, high strength and obvious increases in volume weight.
- It is used to produce a variety of high, medium and low concentration of special NPK compound fertilizers. It is highly adaptable to materials and provides additive-free compression granulation.
- Small equipment size saves site area and engineering cost, as well as equipment cost.
- Normal temperature production; the product is rolled and formed at one time; various parameters can be adjusted.
Wet Granulation
Compared to dry granulation, the pellets processed by wet granulation with high moisture content, so you need subsequent handling of drying, cooling and solidification. The equipment used for the wet granulation process are rotary drum granulator and disc granulator.
- Brief Introduction
Rotary Drum Granulator
- The rotary drum granulator is one of the key equipment in the compound fertilizer industry.
- The main operation way is wet type granulation. Through a certain amount of water or stream, the base fertilizer fully reacts in chemical way in the drum body. Then under certain liquid conditions, the rotating motion of the drum makes the materials particles squeeze together into balls.
- Features
- It is suitable for high-medium-low concentration NPK compound fertilizer.
- Granulation rate up to 70%. There is little amount of returning materials in small size, so you can carry out re-granulation.
- Large production capacity of 1-30t/h.
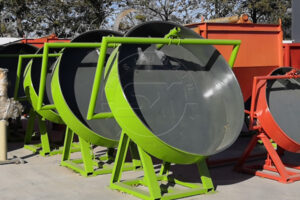
Pan Granulator
· Brief Introducrion
Unlike the drum granulator, which can only produce compound fertilizer, the disc granulator can also process organic fertilizer and is frequently adaptable to both large and small fertilizer manufacturing plants.
Our plant design the disc granulator which transmits powdered materials into the disc by means of the conveyor belt. Under certain humidity conditions, it continuously rolls to form granular fertilizer through the action of centrifugal force, friction, and gravity. Finally, the outlet discharges semi-finished granulars.
- Features
- This granulation equipment is widely suitable for agricultural production in organic and NPK fertilizer production line, and also used in chemical, pharmaceutical, metallurgical, building materials, feed and other industries.
- Simple structure; easy operation; a large selection range of particle diameters; flexible adjustment.
- Low investment cost; 30% lower compared to other pelletizing equipment.
- Production capacity of 0.02-6t/h; granulation rate up to 93%.
- The recipe has limitations, which requires non-viscous materials and is only suitable for low concentration.
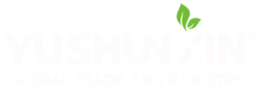
Get Free Quote Now!
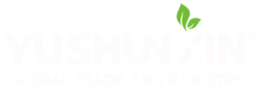